Cummins Engine Secures Heavy Use of Gottwal Port Crane
What should be done to a motor with nearly 25,000 hours of operation to ensure there are no unforeseen breakdowns in the heavy use of a port crane? At the end of 2020, our customer contacted Machinery about this matter. The crane in question is a 140-ton capacity electrically powered Gottwald port crane, with power supplied by a generator.
In this case, the options were to refurbish the original engine or purchase a new one. The customer decided to purchase a new engine, with the old engine being serviced as a spare for the customer. The engine was originally intended to be replaced in the summer of 2021, but the busy port traffic did not allow the crane to be taken out of service in 2021. Machinery stored the engine at its Vantaa branch until the replacement was carried out in early 2022.
The engine in question is a Cummins QST30-G2, a 12-cylinder engine with a displacement of 30 liters. The engine produces 895 kW (1200 hp) at 1800 rpm. The Cummins engine will power the generator providing the power for the electrically operated Gottwald port crane. During the engine replacement, the power package control system was modernized, the generator bearings were replaced, the generator was checked for other aspects, and the flexible coupling between the engine and the generator was replaced. The work was performed at Machinery’s Vantaa engine repair workshop.
To ensure that the new engine is compatible with the old machine control center, the control center was upgraded to a new one. The design took into account in detail the functions and dimensions of the old control center, ensuring that the electrical connections to the existing system were directly compatible. Customer-specific requirements were also considered in the design. A 1000 rpm idle function was added to the engine, which is in use for 5 seconds after the engine starts and for 5 seconds after the engine receives a shutdown command. This significantly extends the lifespan of components such as turbos. The engine was rewired and tested with the new control center at the engine repair workshop. After testing, the engine was delivered to the customer, who carried out the equipment installation at the site.
During the on-site commissioning, alarms and the operation of the machine control system were tested alongside the existing automation system. The commissioning went smoothly, and the customer had already conducted their own testing for 100 operating hours without issues.
News
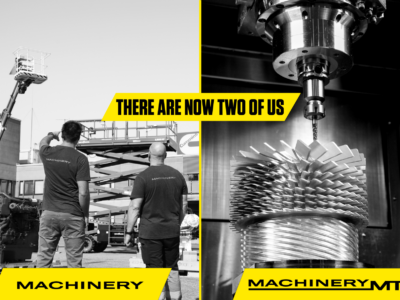
Machinery Ltd will be divided into two independent companies: Machinery Ltd and Machinery MT Ltd – The goal is to enhance customer orientation and simplify internal processes
Read moreNews
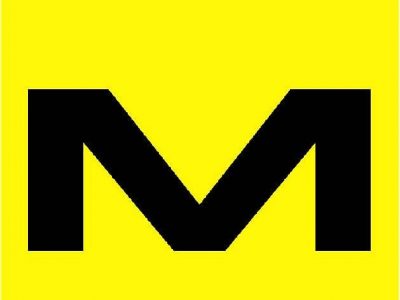
BOREO STREAMLINES ITS ORGANIZATIONAL STRUCTURE TO ENHANCE BUSINESS SERVICE CAPABILITIES
Read more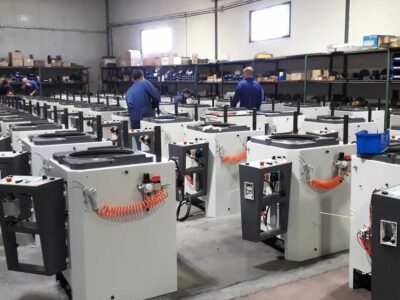